Razor Blades

See, feel, and fly the precision.
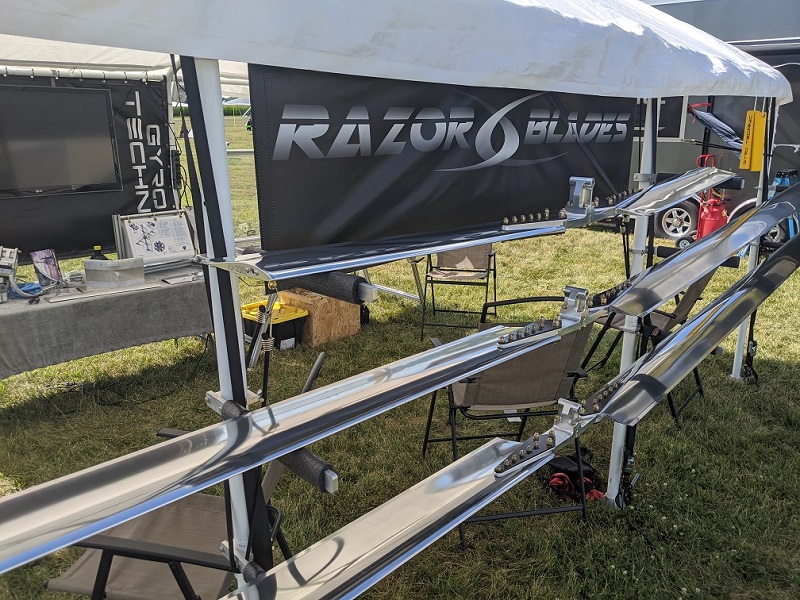
Attention UK / EU Customers!
Razor Blades are now approved and hold a Section T certification for use on many legacy gyro models! (Airworthiness Approval Note: 999-2122)
Razor Blades and other Gyro Technic products can now be purchased through our UK Distributor:
Fly before you buy!
We display at most all the major aviation events! Bensen Days, Sun n Fun, Oshkosh, Mentone, etc: Bring your machine and drop by our display. We typically have blade sets in 23′, 24′ and 25′ diameters for potential customers to demo. Do (did) you fly a legacy set of Dragon Wings with the teeter bolt in the top hole? Razor Blades are a drop-in upgrade! (Standard hub bar features a 3-3/4″ under-slign)
There are no shortcuts! Our aim is to produce the highest quality, most precise rotorcraft blades available. No expense has been spared to assure the precision and quality of these blades.
Blades are designed around an NACA 8H12 profile with reflex and a non-linear twist.
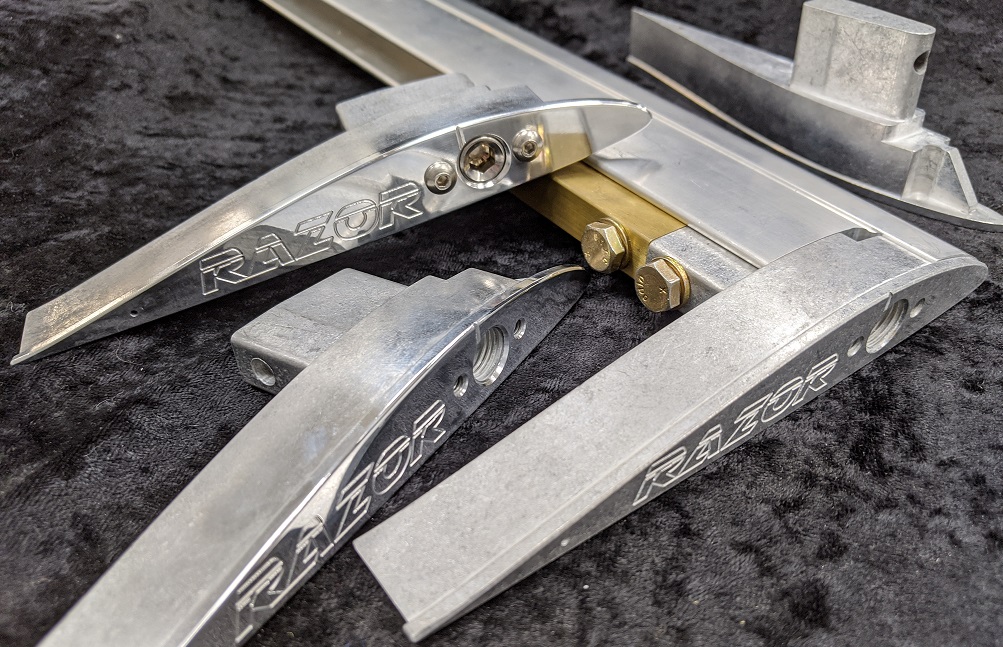
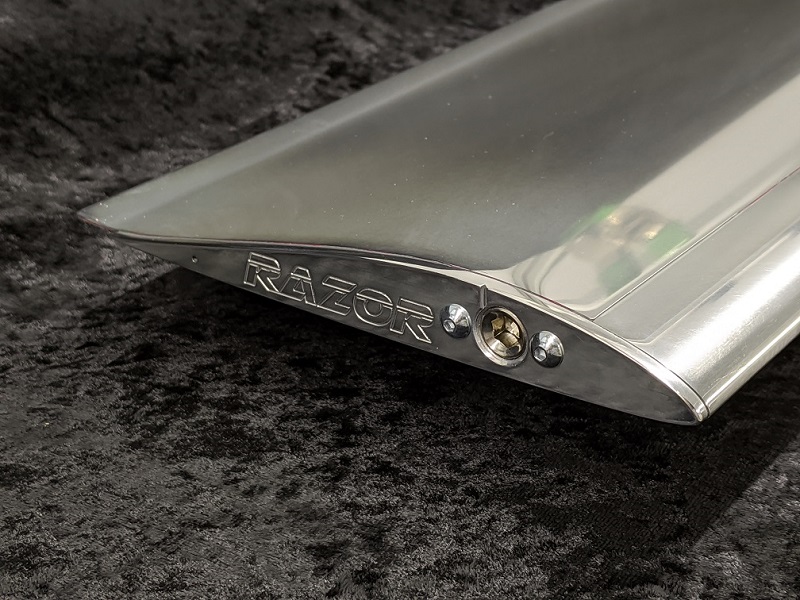
The end caps of Razor Blades are not simply cosmetic or just a way to plug a hole. These parts, as well as the leading-edge extrusions, require extensive machining. The end caps are keyed, bolted, and bonded to the leading-edge profile. This creates an extremely rigid base structure and additional surface area for the aerospace adhesive to bond the aluminum skins around the full perimeter. This dramatically increases the torsional stiffness and integrity of the finished blade assembly!
All components are CNC machined, and therefore precisely identical in size and weight.
The leading-edge extrusions are machined to within .001” in length of each other. The aluminum skins are laser cut to exact size.
Blades are initially balanced to within 1/2 gram. A balancing cavity (plugged with a fine thread set screw) Allows for adding adjustment weights.
An engraved slot up from this cavity hole provides a precise locating feature for blade stringing.
Hub Bars
Our 12″, 24″ & 36″ hub bars features a cylindrical pocket for the teeter block to nest into. Simple tracking adjustment via a setscrew with graduated markings pivot the blade set around the center of the teeter bolt hole, maintaining chord-wise balance of the system!
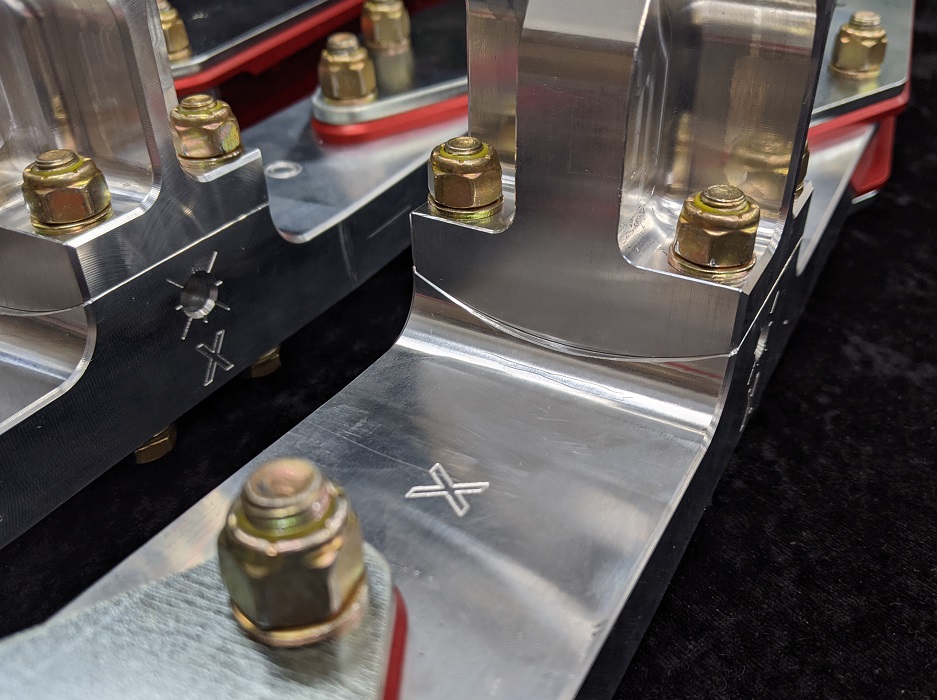
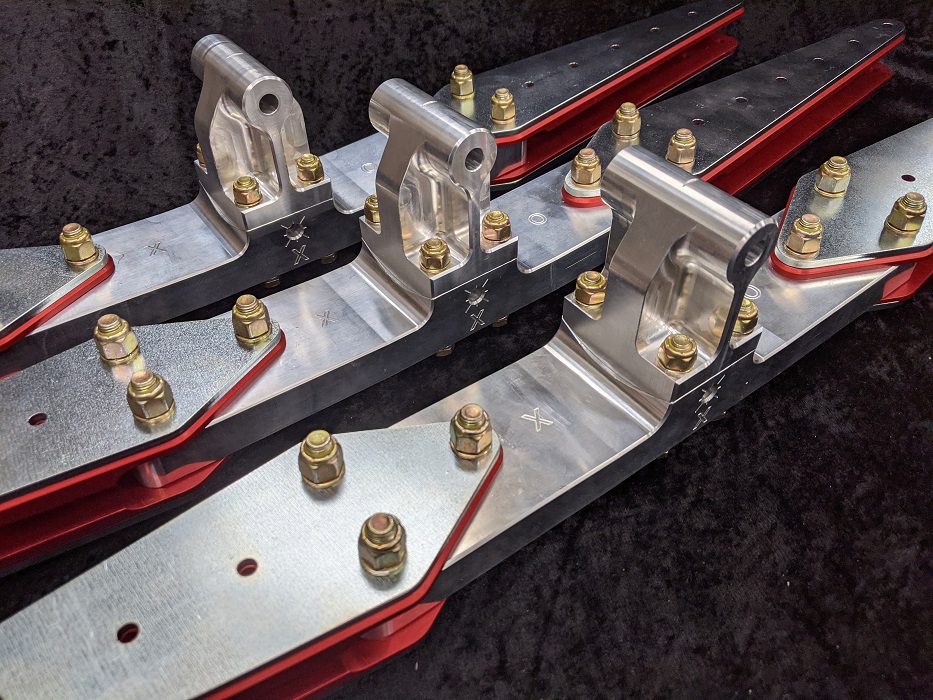
The 2.75° coning angle is precisely machined into the bar.
The blade straps feature the best of both worlds. The aluminum inner spacers are machined to precisely match the airfoil shape for even clamping pressure and secure connection as they lovingly cradle the blades. These are capped by a 3/16″ steel plate, made of a special alloy (80,000 psi), on top and bottom for fatigue resistance.
Razor Blades feature the easiest, most reliable tracking adjustment in the industry! A simple turn of a setscrew will adjust the tracking ever-so-slightly.
A 1/4 turn of the setscrew will change the blade angle by 0.18° (0° 10′ 48″) This would be equivalent of adding a .004″ shim to a competitor’s blade set. A 1/8 turn would be the equivalent of a .002″ shim.
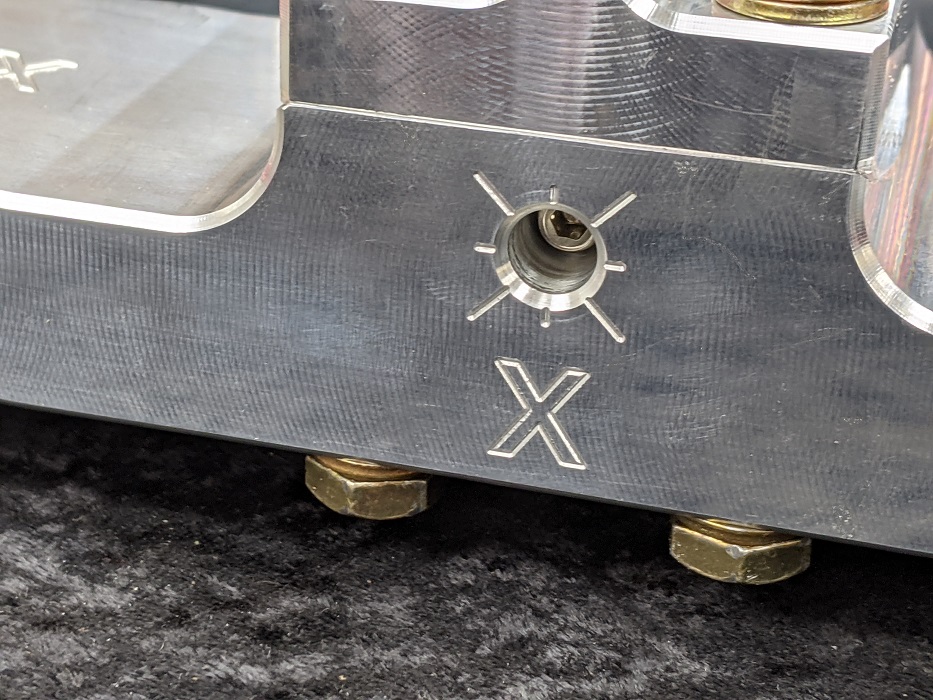
Internal Components and Features
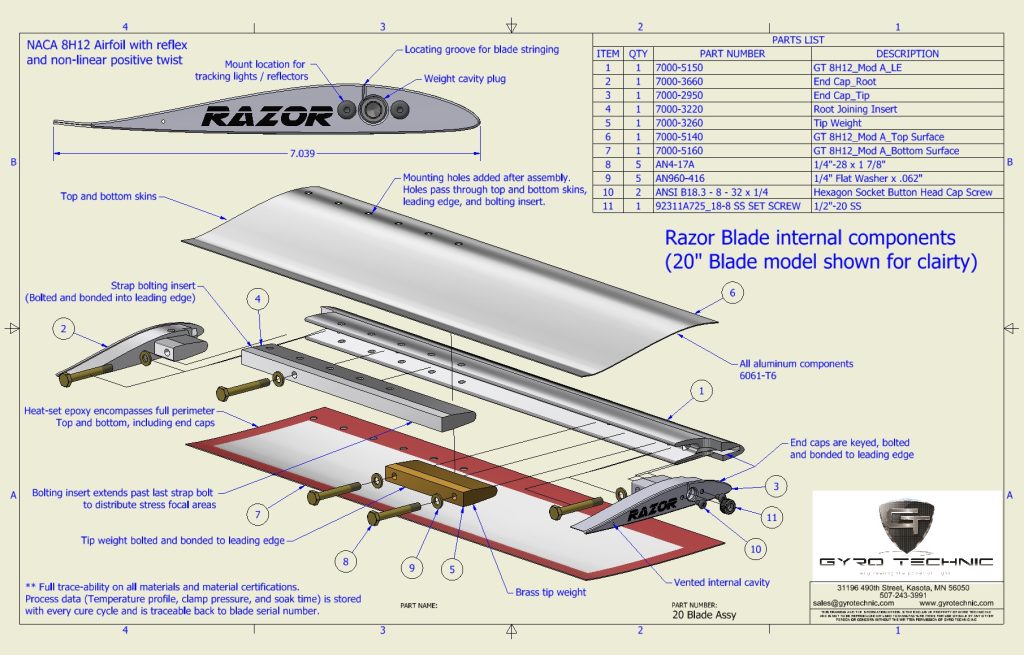
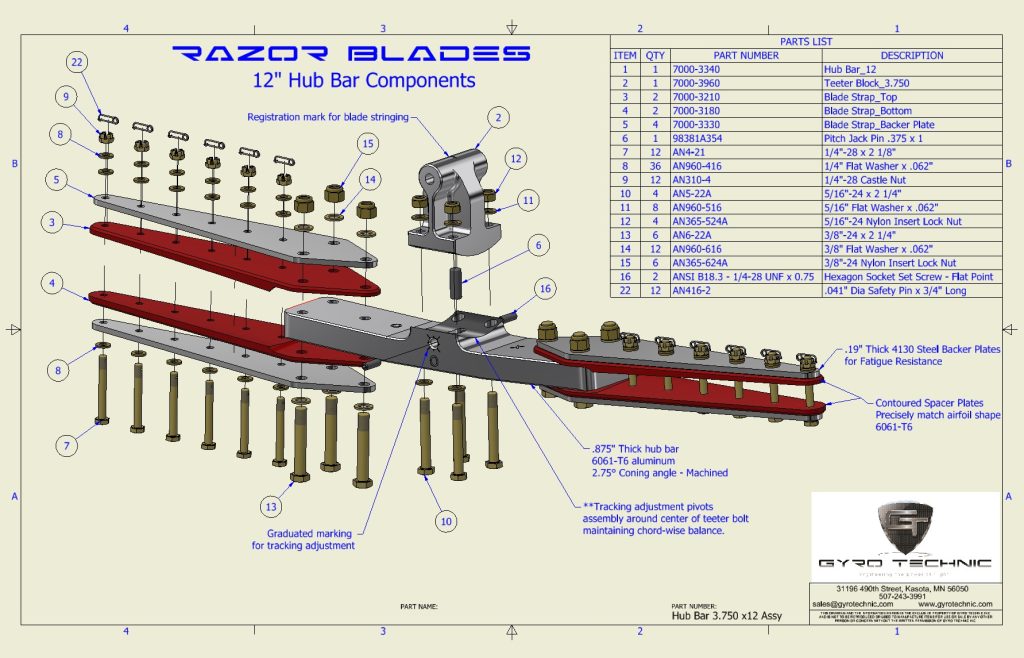
Adhesive Curing
The adhesive is then heat-set in our brand new, high-precision curing oven. The blades are held in precise alignment with clamps that perfectly match the airfoil shape and the non-linear twist, while perfectly even pressure and temperature profile is applied during the curing cycle.
Aluminum expands as it is heated. Each alloy has it’s own coefficient of expansion value. Therefore, the curing fixture is constructed from the same alloy as the blades. A guide system allows the fixture and the blades to expand together (heating), and retract together (cooling), eliminating any shearing forces on the bonded assembly.
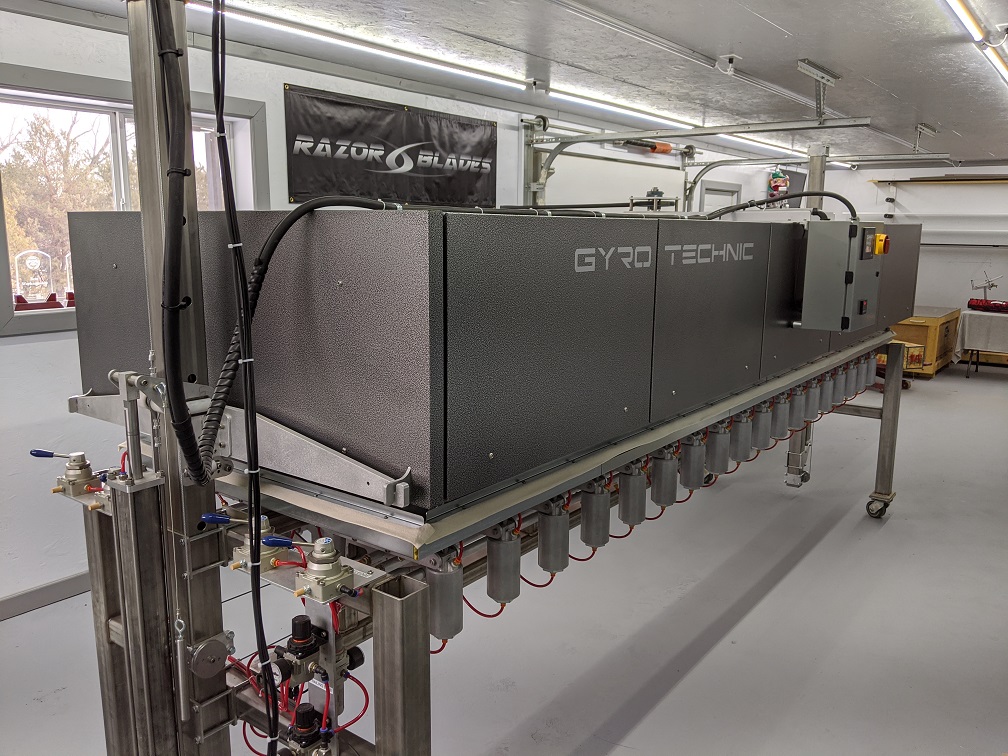
Process Control
Full traceability of process control documentation! All material certifications and process data is collected and saved with every set of blades produced.
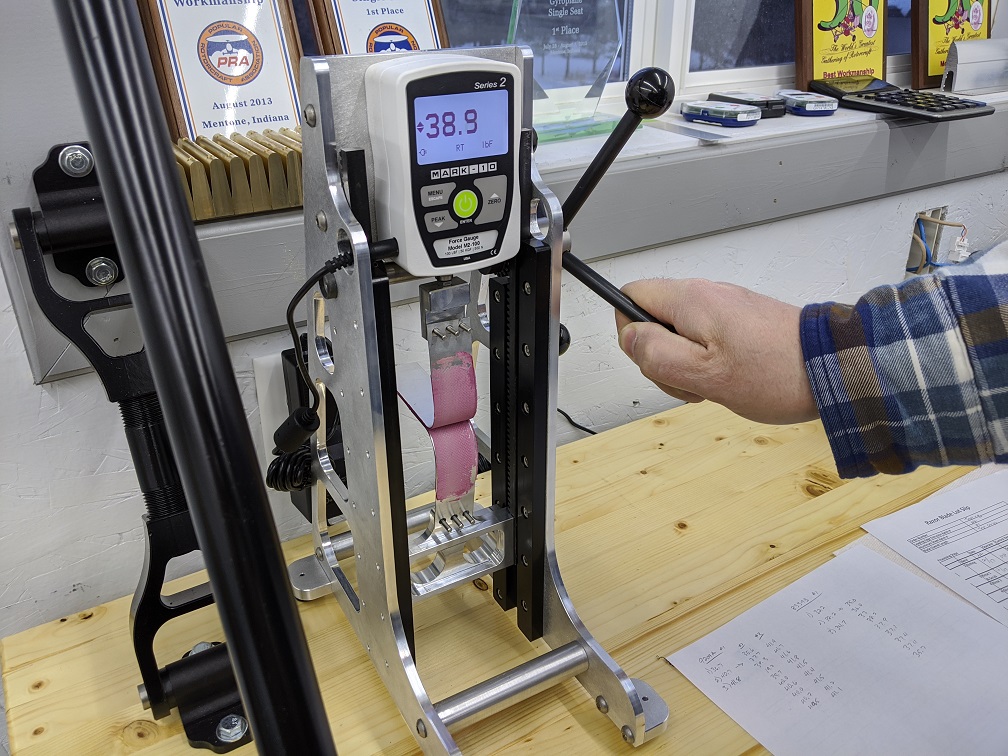
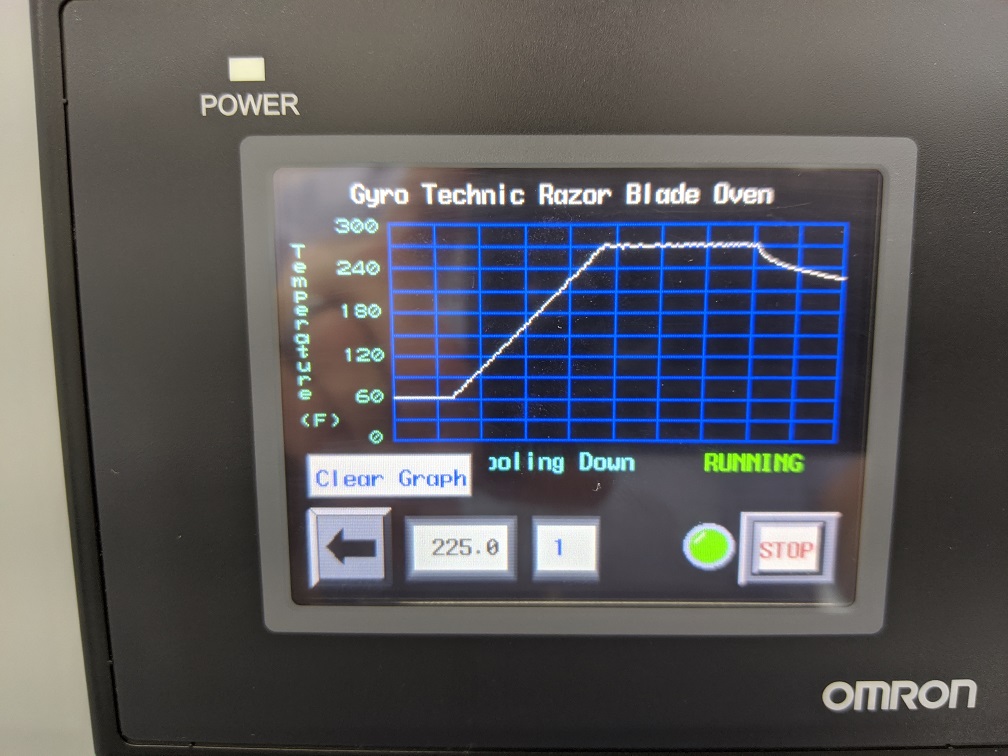
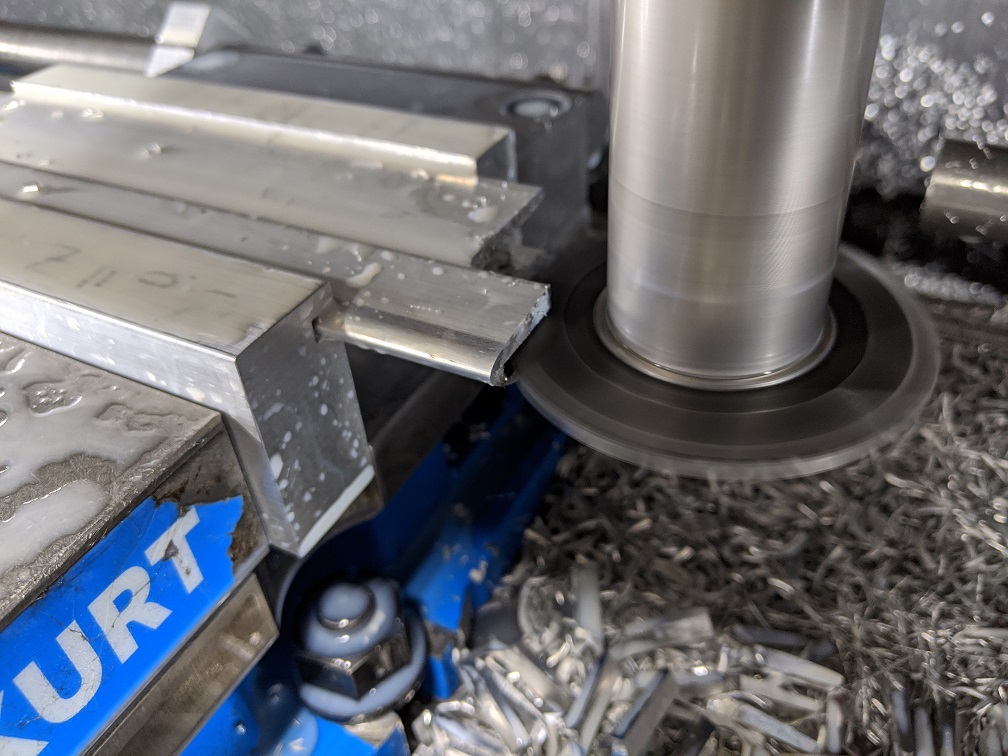
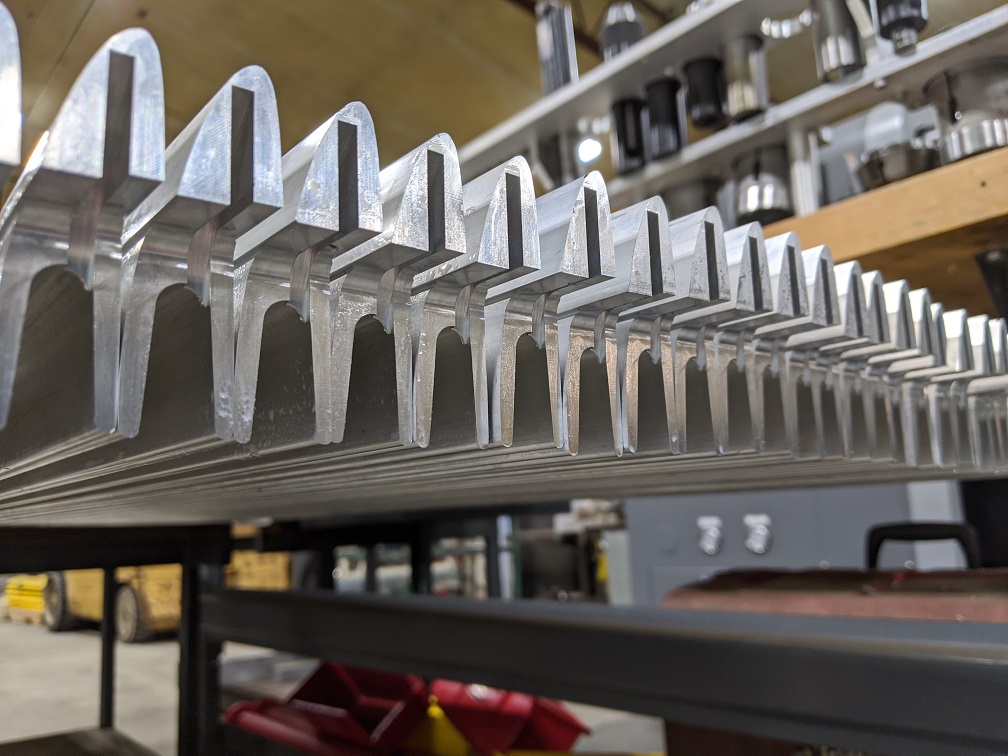
High-Visibility Striping (Optional)
Made from the highest quality, 10-year, cast vinyl. (Choice of Cardinal Red and/or White) These stripes will make your gyro much more visible to other aircraft. Adds a huge margin of safety while looking great at the same time! CNC cut for precision balance and alignment.
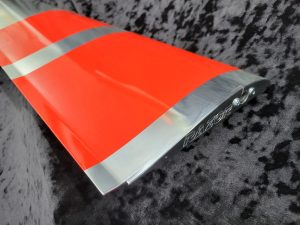
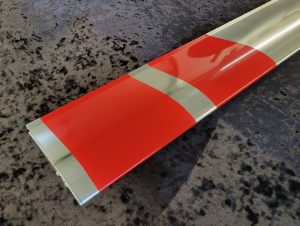
Pre-Rotation
** Note** Razor Blades are not claimed to be “hand start-able”. Not to say it can’t be done if really needed, but it would take great effort. We recommend a good pre-rotator capable of at least 150 RRPM minimum.
See complete manufacturing video HERE!
Call to discuss your application and place an order. 507-933-9033

Pricing and info:
23′ (11′ Blades and 1′ Hub bar) 51.23 lbs $2,650*
24′ (11′ Blades and 2′ Hub bar) 53.79 lbs $2,750*
25′ (12′ Blades and 1′ Hub bar) 54.49 lbs $2,850*
26′ (12′ Blades and 2′ Hub bar) 57.05 lbs $2,950*
27′ (12′ Blades and 3′ Hub bar) 59.61 lbs $3,150*
All crating and packaging expenses included.
*Plus shipping – Contact us for shipping quote. Or, arrange to pick up for free, at one of our many displays across the US!